The Diseb Food Group production lines are busy, with newly imported machines pumping out 25 tonnes of fresh pasta daily.
Today three generations work in the factory, producing a range of Italian-style fresh pasta. As the business has bounced back from disaster, demand from many retailers including major supermarket chains has also grown.
The family is delighted to be back in business, and say during the COVID-19 pandemic, the business has supplied 30 per cent more pasta than its peak two years ago.
“Yes, it is fantastic. It was a big hill to get up and we’re pleased the way it’s come out,” Tony Di Sebastiano explained.
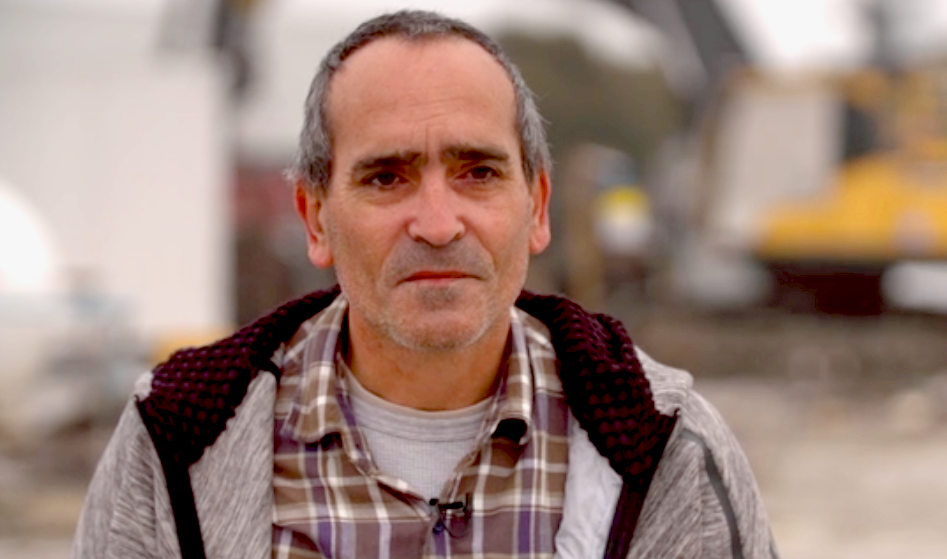
Tony Di Sebastiano is managing director at Diseb Food Group. Source: SBS
“The brand-new machines are the latest technology and allow us to produce product faster, with better quality and food safety as well.”
However, the five production lines that hum eight hours a day lay silent for 18 months after fire tore through their original factory at Somerton, in Melbourne’s north.
Tony Di Sebastiano was among those inside the building when the fire started.
“I always said ‘we can’t ever burn down, with concrete walls, stainless steel machines what can burn?’ Well now we know!” Mr Di Sebastiano said.

The Diseb Somerton factory burning in 2018. Source: Supplied
Diseb had just completed a $2.9 million upgrade with state-of-the-art manufacturing lines, designed to increase output while reducing downtime when fire destroyed the entire building.
The business had more than 50 staff with 26 new hires, including 20 ex-auto workers.
On June third 2018, a fire spread quickly through the factory. Owner Tony Di Sebastiano grabbed an extinguisher and rushed to fight the blaze.
“Then it got too hot. Even fire crews had to stay well back, as the inferno sent black smoke billowing over Melbourne,” he explained.
More than 100 firefighters fought the blaze but the 80 metre by 30 metre building was well alight, and after a concrete wall collapsed it was declared unsound and later demolished.
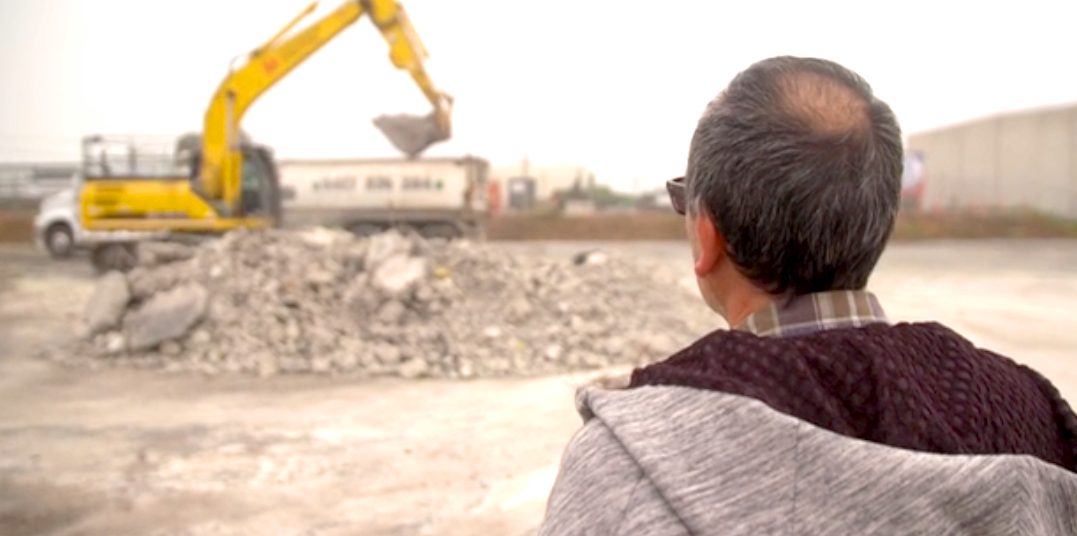
Tony Di Sebastiano watches the demolition of the factory at Somerton. Source: SBS
Along with it, disappeared almost 30 years of hard work and long-cherished hopes for the family’s financial future.
The factory, insured for $3.1 million, was eventually deemed a total loss and a council demolition order requested, so the site could be levelled.
Small Business Secrets visited the demolished site, as Mr Di Sebastiano was picking through the rubble.
“This was our first pasta machine from 1990, has made a lot of pasta,” Tony said crouching next to a burned-out unit.
“It’s very sad actually because we were very excited when this machine first came in.”
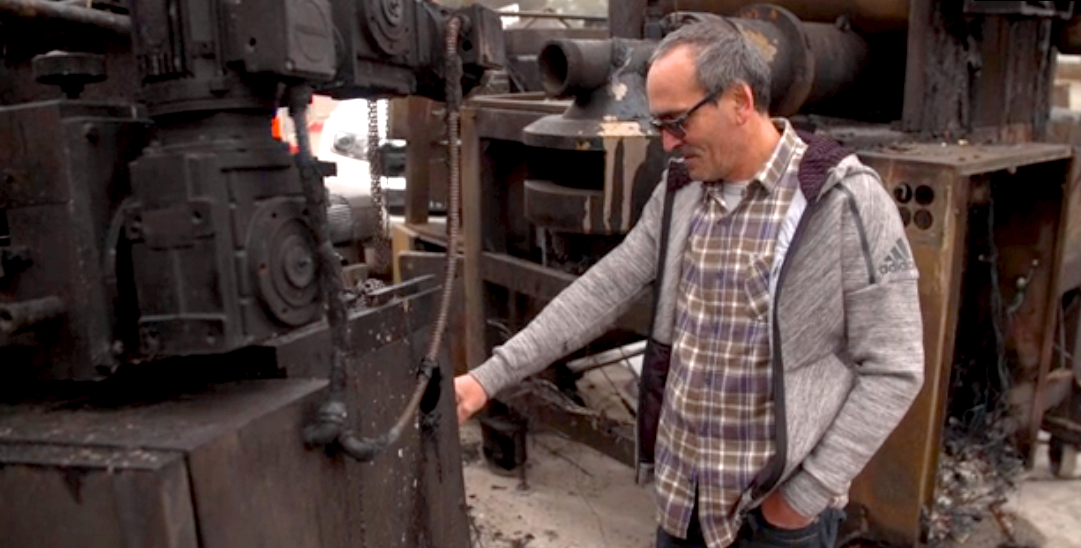
Tony Di Sebastiano with a burned out pasta machine. Source: SBS
After investigators declared the fire ‘accidental’ business insurance made a $750,000 payment, offering an incentive to plan a rebuild.
Ten months later Tony Di Sebastiano was struggling to fund their new start in a different factory, in nearby Epping. Diseb Food Group’s cover eventually provided more than $8.5 million, including payments for damage to the building, business interruption and loss of factory stock and contents. However, there were lessons learned.
“Definitely, on the insurance front you’ve really got to be looking at insurance every time you buy brand new machine,” Mr Di Sebastiano explained.
“We were about 2 million under insured for new machinery, all imported from Europe” he said.
“We were also lucky that we [owned] most of the equipment as interest on bank loans would have prevented us from [using most of the insurance money] to buy new machines.
“So don’t think about trying to save money on insurances. From a business perspective, while you might save some money, if something happens and we know things can happen then you’ll be in trouble.”
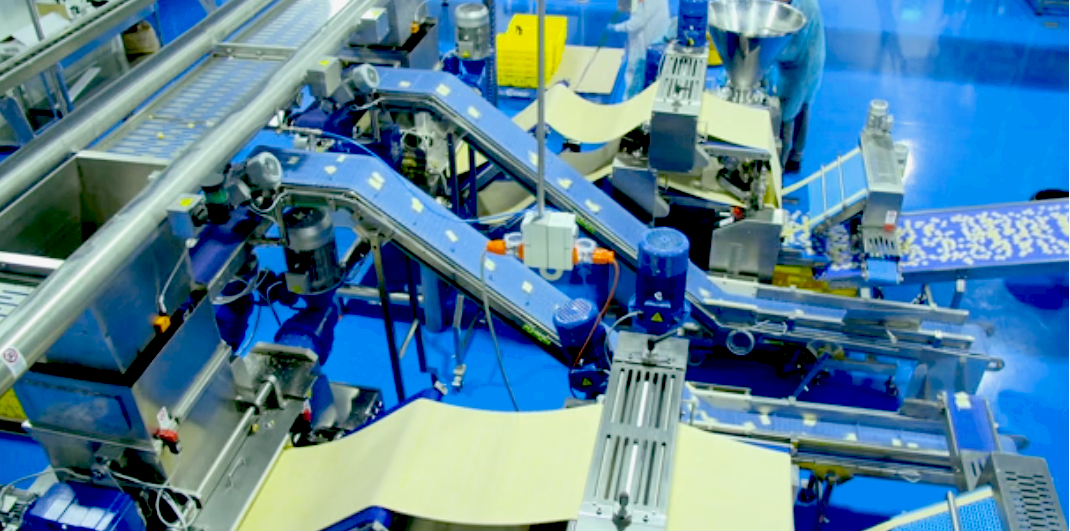
The five new production lines at Diseb run eight hours a day. Source: SBS
The new factory at Epping is now back in full production and the old site at Somerton has also been rebuilt, allowing family to expand their business across two factories.
Beef ravioli remains the most popular item, made according to a secret family recipe handed down the generations.
“It’s made from all-natural ingredients, so what goes in there is beef and spices and fresh vegetables. You couldn’t get any closer to the authentic home-made product,” Managing Director Tony Di Sebastiano said.
“Obviously, it’s been extremely difficult,” he said.
“We’re lucky insurance took care of us and major supermarkets were right behind us.
“But the key thing is external assistance because you can’t do it all yourself.”